Phosphor Bronze PB102 & PB103

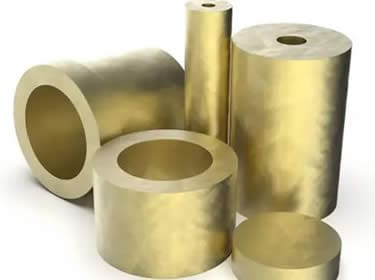
Phosphor Bronze PB102 & PB103: High-Strength Alloys for Demanding Applications
Call 0121 544 5808 Today
Bespoke Manufacturing
Instant Quote Service
Worldwide Delivery
Various Gauges/Thicknesses
Bespoke Manufacturing
Instant Quote Service
Worldwide Delivery
Various Gauges/Thicknesses
What Is Phosphor Bronze PB102 and PB103?
Phosphor Bronze PB102
- Composition: ~5% tin with phosphorus (0.01-0.35%).
- Properties: High strength, fatigue resistance, good corrosion resistance, excellent machinability.
- Applications: Used in electrical connectors, springs, gears, and bushings.
Phosphor Bronze PB103
- Composition: ~8% tin with phosphorus (0.01-0.35%).
- Properties: Higher strength and corrosion resistance than PB102, making it ideal for more demanding environments.
- Applications: Common in marine fittings, pump parts, and pressure vessels.
Benefits of Phosphor Bronze PB102 & PB103 for Buyers
Choosing Phosphor Bronze PB102 and PB103 offers several advantages for buyers across multiple industries:
1. High Strength & Durability:
PB102’s mechanical strength ensures longer-lasting components, reducing the need for frequent replacements and minimising operational downtime.
2. Wear Resistance:
PB102’s ability to withstand friction makes it ideal for moving parts like gears and bushings, enhancing component lifespan.
3. Corrosion Resistance:
Excellent resistance to corrosion in marine and chemical environments, making it a cost-effective solution for long-term use in harsh conditions.
4. Good Electrical Conductivity:
With strong electrical conductivity, PB102 is well-suited for electrical connectors and components, ensuring consistent performance in electrical systems.
5. Machinability:
PB102 can be easily machined, reducing production time and costs, making it a flexible option for manufacturers.
1. Higher Strength:
The increased tin content in PB103 gives it greater strength and toughness, making it ideal for high-load applications in demanding environments.
2. Enhanced Corrosion Resistance:
PB103 offers superior resistance to corrosion, particularly in marine and chemical processing industries, providing longer-lasting performance with minimal maintenance.
3. Wear Resistance:
The alloy’s excellent ability to withstand mechanical wear ensures reliability in gears, bushings, and pressure vessels exposed to friction and high stress.
4. Fatigue Resistance:
PB103’s durability under stress ensures long-term reliability in high-stress environments, reducing the need for frequent maintenance and part replacement.
Cost-Efficiency:
Reduced maintenance costs and longer component life lead to significant savings over time.
Versatility:
Suitable for use in multiple industries, including aerospace, automotive, marine, and chemical processing.
Customisability:
Both alloys can be customised to meet specific application requirements, ensuring optimal performance.
Applications of Phosphor Bronze PB102 & PB103
Both PB102 and PB103 offer excellent durability, wear resistance, and corrosion protection, making them suitable for a wide range of industries:
- PB102: Used in bushings, bearings, and precision springs due to its high fatigue resistance and elasticity.
- PB103: Suitable for parts like pump fittings in aerospace hydraulic systems where high strength and corrosion resistance are essential.
- PB102: Ideal for marine fittings like screws, nuts, and bolts where moderate corrosion resistance is required.
- PB103: Frequently used in marine components like propeller blades, valves, and pumps due to its enhanced corrosion resistance to seawater.
- PB102: Excellent for electrical connectors, terminals, and contacts due to its good electrical conductivity and wear resistance.
- PB103: Used in electrical components that are exposed to harsh environments, providing strength and corrosion protection.
- PB102: Common in gears and fasteners, offering durability and wear resistance under mechanical stress.
- PB103: Preferred for components exposed to high mechanical loads and corrosive conditions.
- PB103: Often used in pressure vessels, pipes, and heat exchangers, offering excellent resistance to chemicals and wear.
Common Challenges of Phosphor Bronze PB102 & PB103
While PB102 and PB103 offer excellent performance, they also come with some challenges or “pain hooks” to consider:
1. Higher Material Costs:
Phosphor Bronze alloys are more expensive than other common metals like brass, making them less ideal for budget-sensitive projects.
2. Limited High-Temperature Performance:
PB102 is not suitable for high-temperature environments, where other materials like stainless steel or nickel alloys may perform better.
3. Work Hardening:
PB102 can become harder to machine as it undergoes work hardening, increasing production costs and time.
1. Even Higher Costs:
PB103 is more expensive than PB102 due to its higher tin content, which may be a drawback for cost-conscious buyers.
2. Machining Difficulty:
The added strength in PB103 makes it more challenging to machine, which can lead to higher tooling and labour costs.
3. Weight Considerations:
PB103’s higher density means it is heavier, making it less ideal for applications where weight is a critical factor, such as aerospace or automotive components.
Industry-Specific Materials Used in Manufacturing
Different industries require specific materials for manufacturing components.
Below are common materials and their applications:
- Steel (Carbon, Alloy, Stainless): Used in construction, automotive, aerospace, and oil & gas for structural components and tools due to its high strength and durability.
- Aluminum Alloys: Lightweight, corrosion-resistant materials used in aerospace, automotive, and electronics industries.
- Phosphor Bronze (PB102, PB103): Preferred in marine, aerospace, automotive, and electrical applications for its wear resistance, fatigue resistance, and corrosion protection.
- Copper & Copper Alloys (Brass, Bronze): Valued in electrical, plumbing, and heat exchanger applications for its conductivity and corrosion resistance.
- Titanium Alloys: Used in aerospace, medical implants, and high-performance automotive parts due to its high strength-to-weight ratio and biocompatibility.
FAQs About Phosphor Bronze PB102 & PB103
What industries use phosphor bronze PB102 and PB103?
What is the difference between PB102 and PB103?
Can phosphor bronze PB102 or PB103 be customised?
Conclusion
Phosphor bronze PB102 and PB103 are essential materials for industries that require high-strength, durable, and corrosion-resistant components. Whether you’re working in aerospace, marine, automotive, or electrical manufacturing, these alloys offer exceptional performance, helping to reduce maintenance costs and extend the lifespan of critical components.
At Stephens Gaskets, we specialise in providing top-quality phosphor bronze materials tailored to your unique specifications.