Laminated Brass

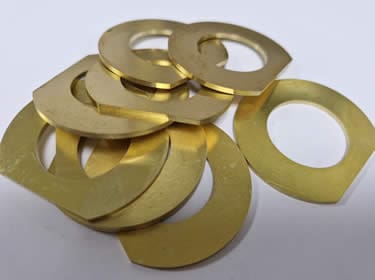
Laminated Brass
Call 0121 544 5808 Today
Bespoke Manufacturing
Instant Quote Service
Worldwide Delivery
Various Gauges/Thicknesses
Bespoke Manufacturing
Instant Quote Service
Worldwide Delivery
Various Gauges/Thicknesses
What is Laminated Brass?
This brass is a versatile composite material made by bonding multiple layers of brass with other materials like copper or steel. This lamination process enhances brass’s natural properties, such as strength, corrosion resistance, and conductivity, making it ideal for various industrial applications.
Its ability to withstand wear, high temperatures, and chemical exposure makes it an essential material in industries that require durability and aesthetic appeal.
Benefits of Laminated Brass
1. Enhanced Strength and Durability
The lamination process improves structural integrity, making laminated brass more durable and better suited for high-stress environments like automotive or machinery parts.
2. Corrosion Resistance
Brass is naturally resistant to corrosion, but laminated brass offers even greater protection in moist, industrial, and marine environments, making it ideal for long-term use.
3. Electrical Conductivity
This brass maintains excellent electrical conductivity, making it a top choice for electrical connectors, terminals, and switches that require both durability and performance.
4. Aesthetic Appeal
Its gold-like finish is often chosen for decorative applications in furniture, plaques, and architectural elements, providing both functionality and a luxurious appearance.
5. Thermal Conductivity
Laminated brass offers excellent thermal conductivity, making it suitable for heat exchangers, radiators, and other systems that require effective heat transfer.
6. Customisability
The lamination process allows for customisation, enabling manufacturers to adjust the material’s strength, thickness, or corrosion resistance to meet specific application requirements.
7. Cost-Effective
This brass can be a more affordable alternative to solid brass or other expensive metals, delivering high performance at a reduced cost.
8. Versatility
It can be used across various sectors, including automotive, aerospace, electronics, and construction, showcasing its multi-functional capabilities.
Applications of Laminated Brass
Laminated brass is widely used in industries that demand a balance of strength, durability, and conductivity.
This brass is ideal for producing gaskets and seals in high-pressure environments, such as engines and pumps, where long-term durability is critical.
Used in electrical connectors, terminals, and switches, this brass combines strength and conductivity to ensure reliable performance in electrical systems.
With its attractive finish, this brass is perfect for plaques, nameplates, and architectural details where both functionality and aesthetic value are required.
In the automotive sector, this brass is found in bearings, bushings, and engine components, thanks to its resistance to wear, friction, and heat.
This brass’s excellent thermal conductivity makes it ideal for heat exchangers and radiators, where efficient heat transfer is essential.
Its resistance to corrosion and harsh environmental conditions makes this brass a top choice for marine components and aerospace parts.
Common Challenges of Laminated Brass
While this brass offers numerous advantages, it is important to be aware of its limitations in certain applications:
- Production Costs
The lamination process can increase manufacturing costs, particularly for custom orders or small batches. - Delamination Risk
In high-stress environments, this brass may experience delamination over time, particularly if exposed to vibration or high-pressure conditions. - Weight
This brass is heavier than other alternatives like aluminium, which can be a drawback in industries where weight reduction is critical, such as aerospace or automotive. - Limited Extreme Environment Use
While durable, laminated brass may not perform well in extremely high temperatures or highly corrosive environments, where stainless steel or titanium may be more appropriate. - Complex Recycling Process
The presence of multiple layers of metals in laminated brass makes recycling more difficult and costly compared to single-metal materials.
FAQs About Laminated Brass
What makes laminated brass different from regular brass?
This brass is made by bonding multiple layers of brass with other metals like copper or steel, enhancing its strength, durability, and corrosion resistance, while maintaining its conductivity and aesthetic appeal.
Where is laminated brass commonly used?
It is widely used in gaskets, electrical components, decorative applications, and automotive parts. Its properties make it suitable for high-pressure environments, corrosive settings, and heat transfer applications.
Can laminated brass be customised?
Yes, this brass can be tailored in terms of thickness, strength, and corrosion resistance to meet specific needs.
How does laminated brass perform in extreme temperatures?
While this brass has good thermal conductivity, it may not be suitable for extremely high-temperature environments where other materials like stainless steel are better suited.
Is laminated brass recyclable?
Why Choose Stephens Gaskets for Laminated Brass?
At Stephens Gaskets, we specialise in producing high-quality laminated brass for a wide range of industries. With decades of expertise, we provide tailored solutions that meet the specific needs of our clients, ensuring durability, performance, and cost-effectiveness.
Our commitment to precision engineering, quick turnaround, and competitive pricing sets us apart in the market.