Plastic Injection Moulding

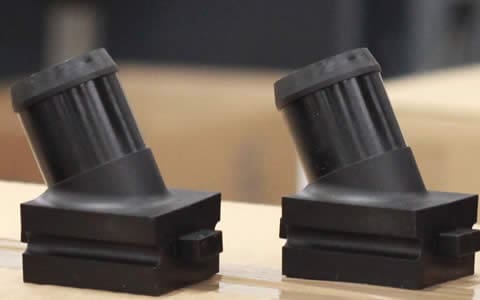
Plastic Injection Moulding Manufacturing Experts & Bespoke Plastic Injection Moulding Specialists
Call 0121 544 5808 Today
Bespoke Manufacturing
Instant Quote Service
Worldwide Delivery
Various Gauges/Thicknesses
Bespoke Manufacturing
Instant Quote Service
Worldwide Delivery
Various Gauges/Thicknesses
Plastic Injection Moulding
Stephens Plastic Mouldings is part of the Stephen Group enterprise. Initially, it was set up as a result of sister company, Stephens Gaskets, buying in plastic shim – which is a plastic moulding. Subsequently, it was decided ‘why buy it when you can make it’. As a result, Stephens Plastic Mouldings was born.
Highly Experienced Team
Furthermore, our team has been manufacturing mouldings for customers for a number of years, and has over twenty years’ experience. Since the inception of Stephens Plastic Mouldings, the business has grown and grown. To begin with, employing two people with us of one machine, there is now a workforce of nine people and thirteen machines. For example, our 350 ton injection moulding machine specially imported from Germany, which has exponentially increased capacity of production. Furthermore, our ability to produce a wider range of components for customers.
Producing a Wide Range of Components
Following on, as part of our growth, we have been able to develop our skills in new and more diverse areas of mouldings. With that in mind, we work with a range of industries from automotive, through to medical uses. Indeed, we are equally dedicated and committed to all stages of the manufacturing and design process. Moreover, our involvement can start at the preliminary design stage of the component.
Beginning To End Service
Therefore, we offer a beginning-to-end service, from the initial design process through to the production of the moulding. Even more, we are able to offer advice on tooling and how best to manufacture the part to keep costs down. As well, we can offer advice on the design process by advising what is achievable on a cost basis.
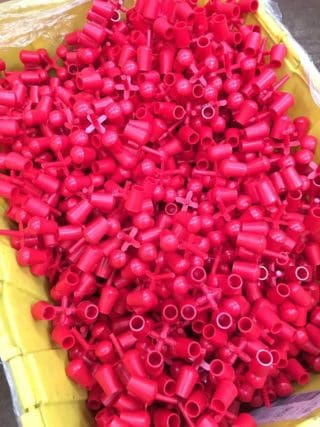
Baseball Cap Face Shield
Furthermore, Stephens Gaskets is supporting the growing demand for PPE by manufacturing plastic face shields. Designed to be clipped onto baseball caps, the visors are made from PET thermoplastic, and are finished with an anti-fog coating.
Face Shields
Stephens Gaskets is responding to the government’s requests for manufacturers to help tackle the growing demand for personal protective equipment during the current coronavirus pandemic.In fact, we are now producing plastic face shields – ideal for employees going back to work.
Supplying a Wide Variety of Industries
So many everyday objects are made by the process of plastic injection moulding, ranging from bottle caps to pieces of furniture.
It should come as no surprise that a number of mechanical parts are manufactured by plastic injection moulding.
For example, car body panels, automotive dashboards, as well as smaller components such as spools are all created using plastic injection moulding.
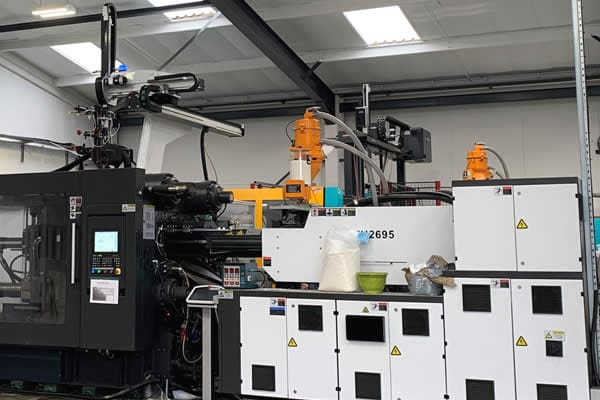
Benefits of Plastic Injection Moulding
- Reduced costs – plastic injection moulders allows for mass production on a very cost-effective scale and means low labour costs
- It’s fast– plastic injection moulding is a fast production method, another factor that helps to reduce costs.
- It’s accurate – a plastic injection mould is produced to the highest levels of precision and often requires minimal finishing.
- Reduced waste – the plastic injection moulding process is extremely efficient as very little of the raw material is scrapped or wasted.
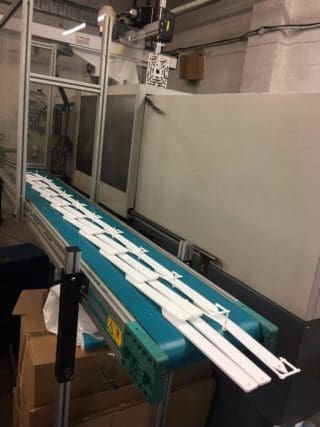
Injection Moulding Process
The process of plastic injection moulding starts with the heating of the material. Markedly, it can be either thermoplastic or thermosetting plastic. Essentially, the material, which starts out as granules, is heated in barrels until the plastic is hot enough to become liquid. From there, it is then directed into mould cavities. Then, once in the mould, the plastic is cooled and allowed to harden into the mould to form the desired component. Additionally, our moulds are designed by industrial designers, which are then produced by mould makers or tool makers using metal, aluminium or steel.
Call Us Today
At Stephens Gaskets, we offer a beginning to end service, from the initial design process through to the production of the plastic mouldings. Furthermore, we can design, create, innovate, manufacture and deliver whatever product you require. Moreover, as a Stephens Gaskets customer, you will benefit from our extensive experience as plastic injection moulding experts as we provide solutions to the continually changing industry.
SALES & GENERAL ENQUIRIES EMAIL sales@stephensgaskets.co.uk
0121 544 5808
All in all, we can offer advice on tooling and how best to manufacture the part to keep costs down. We can also advise on the design process by advising what is achievable on a cost basis.
See www.stephensplasticmouldings.co.uk for more information.
Plastic Injection Moulders at Stephens Gaskets – Everything You Need To Know
Stephen Plastic Mouldings is proud to have spent over twenty years in the industry, designing and manufacturing plastic injection mouldings for an extensive range of industries and clients. While originally starting off small with a team of just two people and one machine, we have expanded over the years to a workforce of nine people and thirteen machines. Equally exciting is our ever increasing production capacity and developing capabilities. Henceforth, our even wider scope of components. Above all, we dedicate ourselves to your project from start to finish. As well, using our expert knowledge will ensure your moulding is rich in quality, efficiency, and won’t let you down.
Plastic Moulders | Experts in the business
Stephens Gaskets has over two decades of experience in the plastic injection moulding industry. As a result, we create high quality moulds and products for a wide range of items. Meanwhile, as leading experts in the industry, we strive to keep up with the continually developing technology. In fact, we have our very own suite of state-of-the-art equipment to help design and manufacture plastic injection moulds to the highest standards. What’s more, plastic moulding is one of the most economical ways of manufacturing products. That is why we offer our services at extremely competitive prices. Finally, with Stephens Gaskets, you can relax knowing we will meet your requirements fast and efficiently without compromising on quality and value.
Plastic Injection Moulding
Stephens Plastic Mouldings is part of the Stephen Group enterprise. It was initially set up as a result of sister company, Stephens Gaskets, buying in plastic shim – which is a plastic moulding. It was decided that why buy it when you can make it. Therefore, Stephens Plastic Mouldings was born.
Highly Experienced Team
Our team has been manufacturing mouldings for customers for a number of years, and has over twenty years’ experience across the team. Since the inception of Stephens Plastic Mouldings, the business has grown and grown. Initially employing two people and one machine there is now a workforce of nine people and thirteen machines. This includes a 350 ton injection moulding machine specially imported from Germany. The machine has exponentially increased capacity of production and ability, to produce a wider range of components for customers.
Producing a Wide Range of Components
As part of our growth, we have been able to develop our skills in new and more diverse areas of mouldings. These range from automotive, through to medical uses. We are equally dedicated and committed to all stages of the manufacturing and design process. Our involvement can start at the preliminary design stage of the component.
Beginning To End Service
We therefore offer a beginning-to-end service, from the initial design process through to the production of the moulding. Within this, we are able to offer advice on tooling and how best to manufacture the part to keep costs down. As well, we can offer advice on the design process by advising what is achievable on a cost basis.
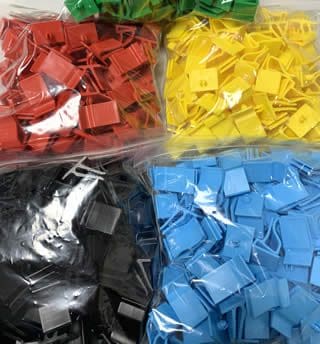
Baseball Cap Face Shield
Stephens Gaskets is supporting the growing demand for PPE by manufacturing plastic face shields. Designed to be clipped onto baseball caps, the visors are made from PET thermoplastic, and are finished with an anti-fog coating.
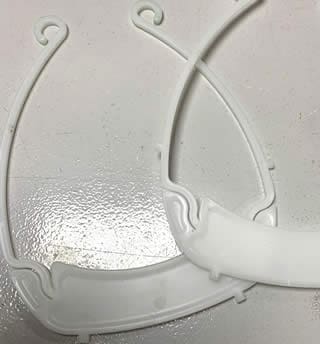
Face Shields
Stephens Gaskets is responding to the government’s requests for manufacturers to help tackle the growing demand for personal protective equipment during the current coronavirus pandemic. We are now producing plastic face shields – ideal for employees going back to work.
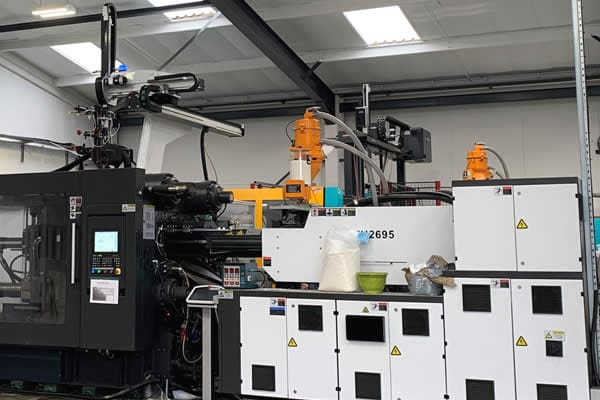
Supplying a Wide Variety of Industries
So many everyday objects are made by the process of plastic injection moulding, ranging from bottle caps to pieces of furniture. In the industry, a number of mechanical parts are manufactured by plastic injection moulding. These include car body panels, automotive dashboards, as well as smaller components such as spools are all created using plastic injection moulding.
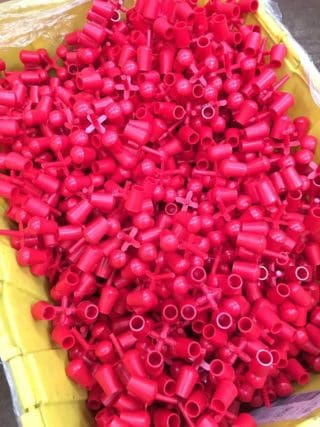
Benefits of Plastic Injection Moulding
- Reduced costs – plastic injection moulders allows for mass production on a very cost-effective scale and means low labour costs
- It’s fast– plastic injection moulding is a fast production method, another factor that helps to reduce costs.
- It’s accurate – a plastic injection mould is produced to the highest levels of precision and often requires minimal finishing.
- Reduced waste – the plastic injection moulding process is extremely efficient as very little of the raw material is scrapped or wasted.
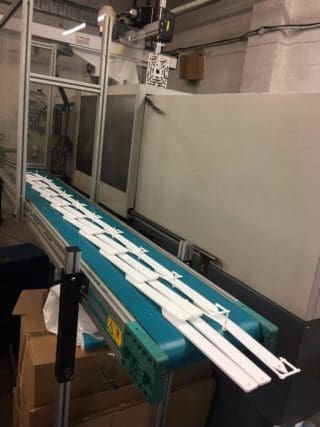
Injection Moulding Process
The process of plastic injection moulding starts with the heating of the material. The material can be either thermoplastic or thermosetting plastic. The material, which starts out as granules, are heated in barrels until the plastic is hot enough to become liquid. In liquid form, it is then directed into mould cavities. Once in the mould, the plastic is cooled and allowed to harden into the mould to form the desired component. Moulds are designed by industrial designers, which are then produced by mould makers or tool makers using metal, aluminium or steel.
Call Us Today
At Stephens Gaskets, we offer a beginning to end service, from the initial design process through to the production of the plastic mouldings. We can design, create, innovate, manufacture and deliver whatever product you require. As a Stephens Gaskets customer, you will benefit from our extensive experience as plastic injection moulding experts as we provide solutions to the continually changing industry.
0121 544 5808
We can offer advice on tooling and how best to manufacture the part to keep costs down. We can also advise on the design process by advising what is achievable on a cost basis.
See www.stephensplasticmouldings.co.uk for more information.
Plastic Injection Moulders at Stephens Gaskets – Everything You Need To Know
Stephen Plastic Mouldings are proud to have spent over twenty years in the industry, designing and manufacturing plastic injection mouldings for an extensive range of industries and clients. While originally starting off small with a team of just two people and one machine, we have expanded over the years to a workforce of nine people and thirteen machines. In this time, we have increased our capacity of production alongside developing our capabilities. We can now produce an even wider scope of components. We dedicate ourselves to your project from start to finish. As well, using our expert knowledge will ensure your moulding is rich in quality, efficiency, and won’t let you down.
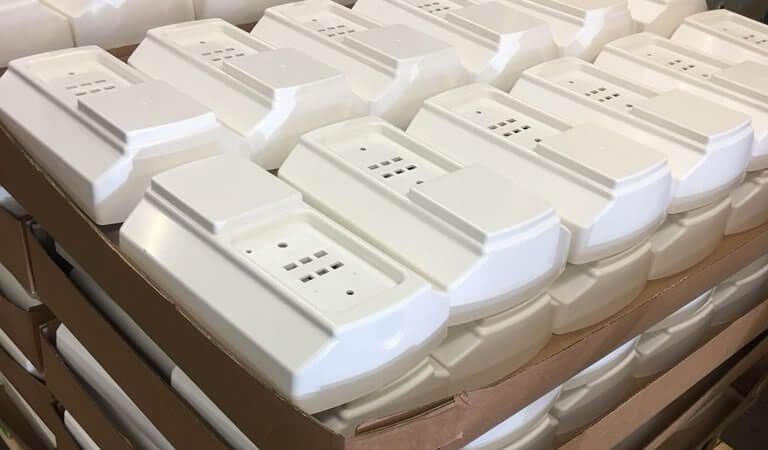
Plastic Moulders | Experts in the business
Stephens Gaskets has over two decades of experience in the plastic injection moulding industry. We create high quality moulds and products for a wide range of products. As leading experts in the industry, we strive to keep up with the continually developing technology. We have our very own suite of state-of-the-art equipment to help design and manufacture plastic injection moulds to the highest standards. Plastic moulding is one of the most economical ways of manufacturing products. This is why we offer our services at extremely competitive prices. With Stephens Gaskets, you can relax knowing we will meet your requirements fast and efficiently without compromising on quality and value.